Preparing your digital artwork files for offset printing can seem a daunting task. We walk you through everything you need to know to make the process easy and effective while avoiding the most common mistakes
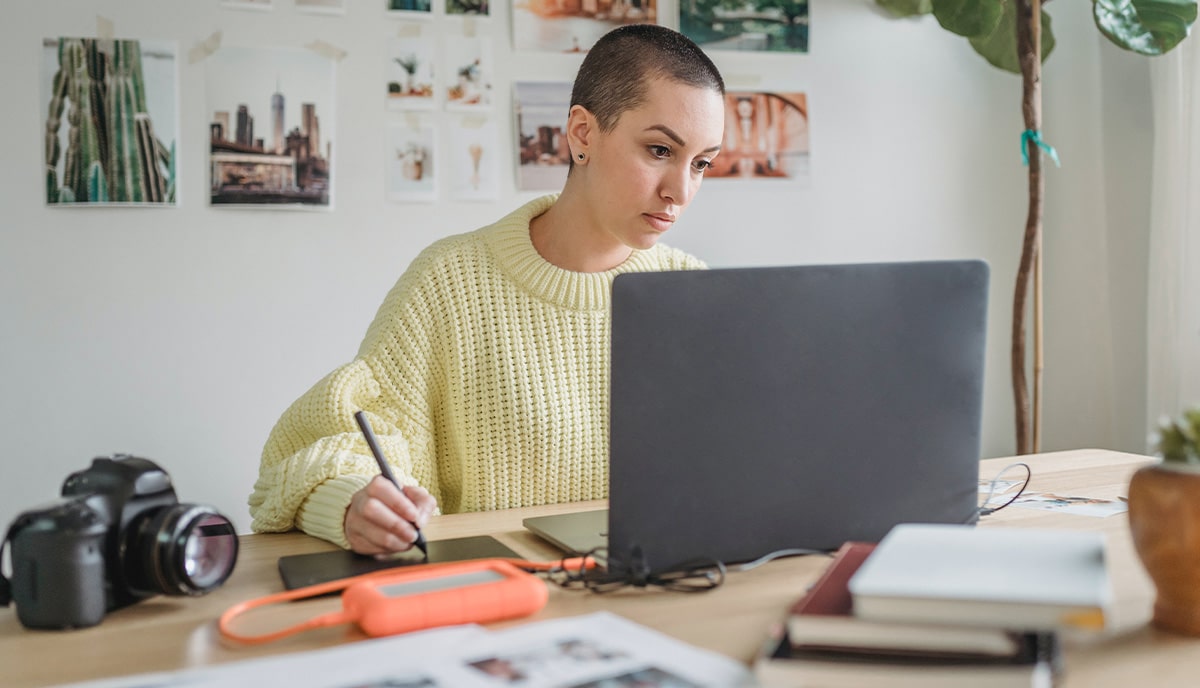
Photo by George Milton via Pexels.com
There are two very different skill sets required in producing artwork for printed products. Not so long ago a graphic designer and an artist were totally different roles, but in recent years the boundaries have blurred and increasing numbers of independent creatives from other fields—marketers, self-published writers, educationalists, and events promoters, for example—are taking on the role of both artist and designer when preparing their materials for print. Today’s designers—professional or otherwise—need a good understanding of what is required to take a creative concept through to printed completion, avoiding all the possible complications. So, let’s walk you through what you need to know.
Choose the right design software
Using professional page make-up software is the first, and most important, step in the process. Adobe products such as Illustrator, Photoshop, InDesign and others such as QuarkXPress are the industry standards and have an established track record for creating professional, print-ready files.
There are a host of free programs or cheaper options than these packages but, if you are after consistent, well-produced results, stick with the software all offset printers will have and use every day.
If you are unsure as to how to prepare your files or set up a particular aspect of a job, just call us up and ask! An expert from our pre-press department will happily talk you through it. In fact, speaking from experience, the closer the relationship between the designer/artist and the pre-press department, the smoother the process will run. That’s why we always say that it’s never too soon to get your printer involved. For example, we can support and advise you with all technical aspects of the design process besides helping you decide which paper stock, weights, coatings, and finishes, not mention binding options, may be most appropriate for your project. All these things can impact design, so it’s best to figure them out in advance to save everyone a lot of time and heartache later.
One thing we will say, though, is that even if you’re working on a restricted budget, avoid the free software that comes on your PC or Mac. Yes, it will work fine for cranking out the invitations to your Christmas party printed on your own home machine, but for producing high-quality, print-ready PDFs, forget it. Invest in the best. Word, Publisher and others may be widely used but they are not designed for professional printing work and you’ll only need to convert all the files later if you try.
Understand and adjust the "color space"
If you are new to preparing artwork for printing, there is a lot to learn!
First of all, dismiss from your mind the idea that what you see on your computer screen in will be what appears in print nicely packaged a few days later in your office or on the doorstep. Unless you have a good grasp of the influencing factors, you may be disappointed with the results. Color (or Colour) management is crucial and a difficult area to fully understand without professional training, even to those with plenty of experience in the trade. Not so long ago this meant producing Photoshop images with various color profiles attached or embedded that carried this information through to the RIP (Raster Image Processor).
This interprets the file information and converts it via Postscript into a format that can be output to various devices including plates for offset litho. Luckily you don’t actually have to understand how this all works. Still, it’s good to get a grasp of the basic of color spaces and how to set them up in your files ready for printing. So, here we go.
CMYK and RGB color spaces
You may notice that the major software platforms work in various color spaces.
All you really need to know is that RGB (Red Green Blue) is the additive color space for anything produced for and viewed on a screen. CMYK (Cyan Magenta Yellow Black) are the basic inks used in the subtractive offset print process. Therefore, make sure you are working in CMYK when producing images in Photoshop or similar graphics packages.
Note: Photoshop and other image software normally work in RGB as a default, so you will have to convert your files. There are two other important factors to be addressed when using images in your project.
High-quality printing and high-resolution photos
If you’re not sure what image resolution is, it’s the pixel count or dpi (dots-per-inch) of the photo file. You’ll have seen examples of low-resolution images being printed, and they look horrible; they are often blurry or “pixilated”. The problem is that a computer monitor, phone or other device, only requires a resolution of 72 dpi for an image or text to look sharp and clear. Offset printing, however, needs your images to be at least 300 dpi, and this is if reproducing at 100% in the software. If you are enlarging the image in your program, the proportional resolution will drop accordingly.
For mono bitmap line drawings and graphics, the resolution may need to be nearer 1000dpi for accurate reproduction. If all this seems complicated, well it is, but if you ensure your images are CMYK and 300dpi, you are heading in the right direction.
Your files need to be saved in certain formats, for example, EPS, JPEG, TIFF etc. The differences between these types and why and when to use them are beyond the scope of the this post, but the various formats retain different information, much of it not really visible to the eye. JPEG files compress the data, creating much smaller files but losing some of the color information and detail, for example.
Modern RIPs and page make-up software sort out a lot of the problems for us now; files that we couldn’t have worked with a few years ago, we can now process, although the results may vary. As with images, imported graphics such as vector logos and anything else not created in the software itself need to be CMYK as well.
If using InDesign, Illustrator or QuarkXPress, set up color breakdowns in the job as CMYK for the best results. So far, reasonably straightforward. But again, if you have questions, ask. We pride ourselves on being as helpful as possible.
Pantone color printing
One of the areas that commonly causes problems with offset printing jobs is where special colors, spot varnishes and other non-CMYK features are involved. For example, a client’s logo needs to be printed as a special Pantone color rather than out of CMYK. However, it may have been supplied as an RGB file that will print in totally the wrong color. Or the Pantone reference number in the supplied file may not match with the Pantone number in InDesign.
It will look alright on the screen or even print well on your office printer, but may not separate correctly at the pre-press stage. The only way to check this is to open every element of the job in its native format and make sure each aspect is correct. If you are setting up elements of a job for spot varnishing or foiling etc, and you’re not already 100% sure of what you’re doing, please talk to our pre-press department. This is a potentially complicated area and the initial job set up is crucial. Getting it right now saves you time and money down the line. So, talk to us and let us make sure everything’s in order right from the get-go.
Rich black ink set up
The design of the print project can have an impact on the final result as offset printing does have certain limitations which can mean results can vary. Heavy ink loads on dark solid colors can cause issues as can the reproduction of some gradients and vignettes. Solid black printing, in particular, needs to be set up correctly in the first place to ensure a rich result.
There is a reason why CMYK printing is generally cheaper and that’s because it’s a simpler process in many ways. We separate everything into the four process colors and then recombine them on the presses. As soon as other separations are required, the process becomes more involved.
Once you are happy with the design of your project and the artwork is complete, you need to produce print-ready files. InDesign, Illustrator and Quark have pre-sets to create high resolution, print-ready PDF files. These will include the appropriate bleed and trim marks required.
Talk to us!
The bottom line is to let us help you! Get in touch today—either by telephone, email, Skype, or our simple contact form—to chat through your needs or to ask for a no-obligation quote. We can’t wait to help you make your next print project one that exceeds all your former expectations.